AGRICULTURE AND CANNABIS
Maximize Grams per sq/ft and Minimize Scrap
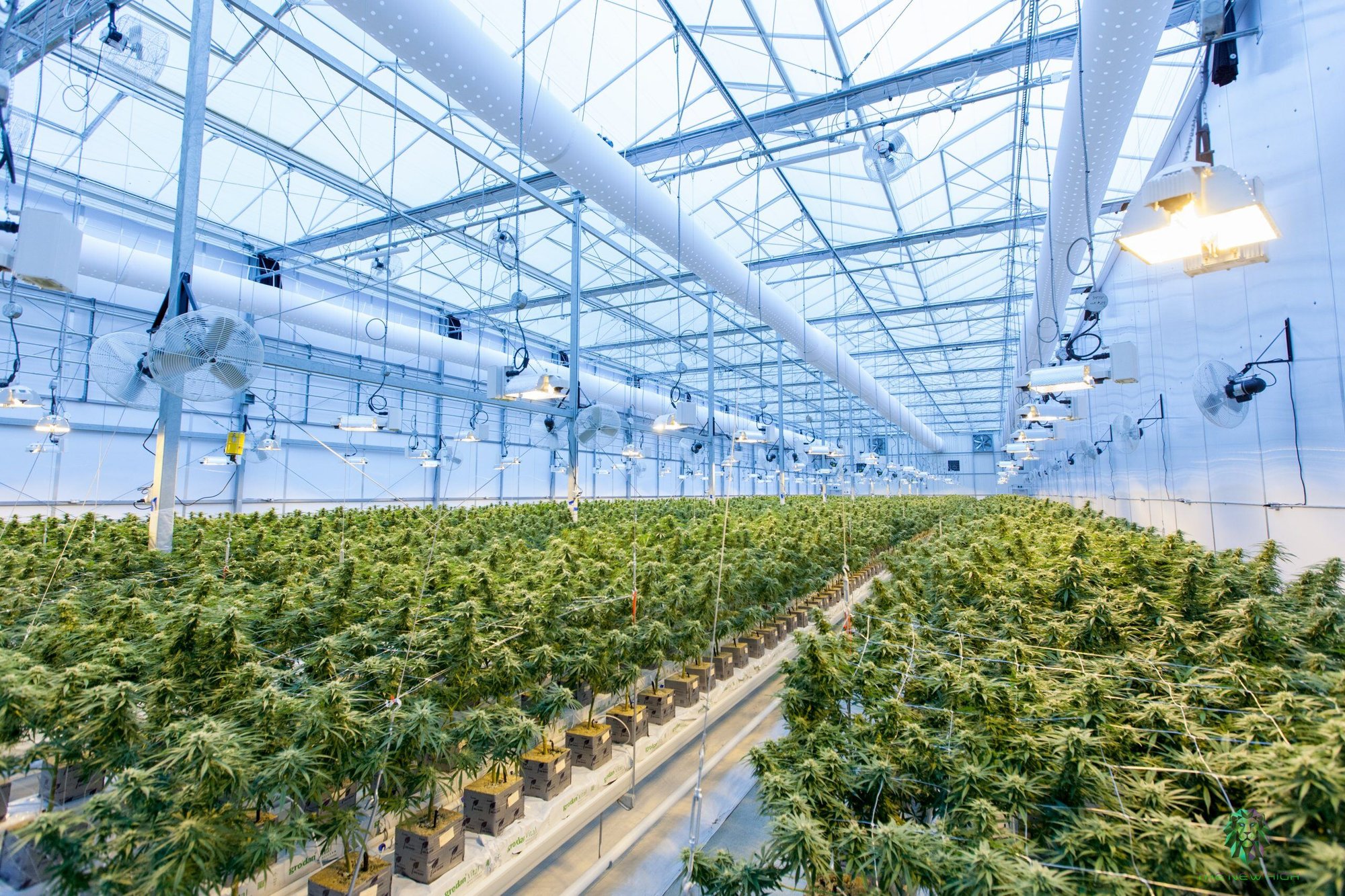
AGRICULTURE AND CANNABIS
Reduction in Downtime
Increase Agility
Operator Empowerment
The DecisionEngine integrates predictive and prescriptive AI models to deliver real-time insights to operators on the shop floor. By analyzing key factors such as machine performance, raw material prices, and quality data, the DecisionEngine provides operators with specific actions to take, thereby removing the cognitive load of diagnosing problems. This has several important benefits including reduction in downtime and scrap, and leads to operator empowerment.
DecisionEngine Features
Predictive Analytics
Prescriptive Guidance
Real-Time Data Integration
PRODUCT OVERVIEW
Manufacturing operations are complex, with production systems constantly responding to changing business and market conditions. This white paper introduces our AI-driven DecisionEngine, which simplifies the operator’s job and improves business outcomes by optimizing production decisions in real time.
By leveraging predictive and prescriptive AI, this technology drives significant financial benefits through reduced scrap, minimized downtime, and better decision-making. With real-time integration into Quality Management Systems (QMS) and Enterprise Resource Planning (ERP) systems, the DecisionEngine delivers actionable insights across the business.
AI-POWERED SOLUTION
In today’s manufacturing landscape, the ability to respond quickly and efficiently to changing business needs is critical. However, traditional shop floor processes often struggle with this dynamic environment. Operators must not only understand their machines but also consider the broader business context, something that is rarely part of their training. To bridge this gap, we developed the DecisionEngine, an AI-powered solution that automates decision-making on the shop floor, enabling faster, more informed responses to real-time changes in production environments.
DecisionEngine uses advanced AI algorithms to reduce the burden on human operators, shifting the process from a traditional "Diagnose > Decide > Decision" model to a streamlined "ACT" model. This technology improves consistency in operations, reduces downtime, and limits production waste, all while ensuring that the operator makes optimal decisions based on the most current data.
SOLVING PROBLEMS
Manufacturing operators are typically trained to run machines but not necessarily trained to understand the broader implications of their actions on business outcomes.
Factors like fluctuating raw material costs, shifts in demand, and internal process variations often go unnoticed by operators, even though they can have a significant impact on financial performance.